The objective of the project was to improve the safety and functionality of research labs on campus with the primary goals of increasing energy efficiency, creating utility cost savings, and ultimately reducing the Institute’s carbon footprint.
Fume hoods, snorkels, valve actuators, and purge buttons are all vital components of a research lab that allow research efforts to be conducted safely and efficiently. And recently, these components have either been added or upgraded in 150 labs located in the Ford Environmental Science & Technology (ES&T) and the U.A. Whitaker Biomedical Engineering (UAW) buildings as part of the Facilities Management Lab Ventilation Project. The objective of the project was to improve the safety and functionality of research labs on campus with the primary goals of increasing energy efficiency, creating utility cost savings, and ultimately reducing the Institute’s carbon footprint.
The project is already proving successful. On average, the airflows in ES&T have been reduced by more than 70% and more than 50% in U.A. Whitaker, and according to the most recent performance reports, substantial cost savings have already been measured. Saving energy and saving money is a win-win for Georgia Tech.
According to the American Society of Heating, Refrigerating, and Air Conditioning Engineers, laboratory space is considered one of the highest energy intensive spaces on a college campus. Combine that with high maintenance costs, and it’s easy to see why research labs would be a target when searching for campus efficiencies and savings. Several years ago, Georgia Tech Facilities engineers visited the nationally recognized Smart Labs program at the University of California at Irvine and brought back an outline on how to implement the same type of program here on campus.
Securing funding for the project was the crucial first step. This project qualified for a Guaranteed Energy Savings Performance Contract, which means that Georgia Tech did not have to provide funds up front. Instead, an outside contractor is hired, the contract is signed, the work is completed, and the contractor gets paid back when the project is successfully operating. Then — cost savings materialize.
With more than 400 research labs on campus, why did the project planners choose Ford ES&T and U.A. Whitaker?
“Prior to the project, we calculated that six buildings in the BioQuad district comprise 5% of the campus by square foot but nearly 30% of the energy use. Of those buildings, only UAW and Ford ES&T were eligible for the project as Georgia Tech-owned buildings,” explained Greg Spiro, senior mechanical engineer, Design and Construction.
Spiro managed the project from the contractor selection through the audit stage, which was essentially a trial run and safety analysis in each building. The next and most important step was engaging the researchers who worked in the specified labs.
Spiro added that the biggest obstacle was managing all of the end users, as the project required vacating all research labs for a week at a time. Researchers had to believe in the project in order to willingly give up lab access and have their research interrupted. That’s where Kynthia Gaines, construction project manager, served a key role.
“Early in the process we put together a robust communication plan that included the project website, periodic town hall meetings, and one-on-one meetings with each primary investigator (PI),” Gaines said. “Also, we received support from Executive Vice President for Research Chaoukie Abdallah. This backing helped alleviate some of the hesitation the PIs experienced about the process.”
Nazia Zakir, assistant vice president, and Ryan Lisk, lab and chemical safety officer, of Environmental Health and Safety were also heavily involved throughout the project. Pre-construction lab visits were critical to determine any needs for the storage or removal of special chemicals.
The project began in August 2019 and committed to a strict 13-month schedule. The plan concentrated efforts by moving through each building floor by floor. All 150 labs were complete by July of this year despite the emergence of the coronavirus. With some researchers not on campus and their labs not active, the project was able to progress more quickly than originally planned.
Pamela Pollet, senior academic professional in the School of Chemistry and Biochemistry, says that for her lab, the renovation process was smooth and effective. “We had to adapt a little bit to the new system but it took perhaps a week or two.”
The 150 Smart Labs now feature consistent pressure and temperature controls for better workspaces, safer environmental conditions, purge buttons for the release of chemicals, and on-site technical support and preventive maintenance.
“In a word, the reason these labs are so expensive to operate is air,” Spiro said. “The energy savings measures are aimed at providing the right amount of ventilation.”
And with cost and energy savings exceeding expectations, both Greg Spiro and Kynthia Gaines look forward to future projects on campus, with labs in the Petit Institute for Bioengineering and Bioscience potentially at the top of the list.
For more information, visit facitlities.gatech.edu/lab-vent.
Additional Images
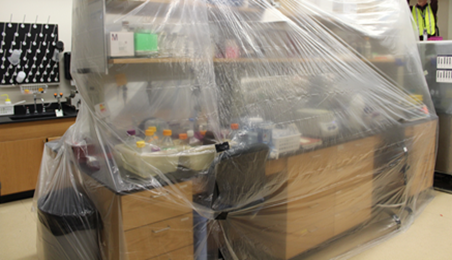